Top 10 Safety Protocols for Secure LPG Plant Operations
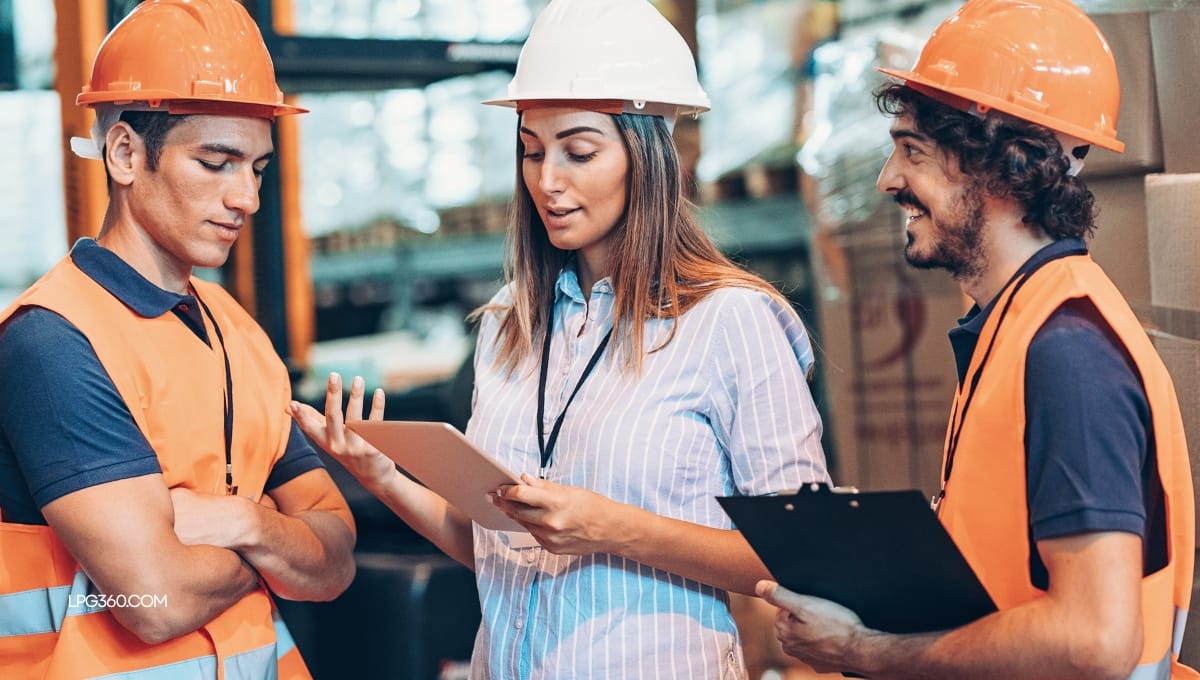
Liquefied Petroleum Gas (LPG) is a widely used energy source in industries and households. However, due to its highly flammable nature, handling and storing LPG requires strict safety measures. A single leak or improper procedure can result in catastrophic accidents. LPG plant operators must implement comprehensive safety protocols to ensure workplace security, employee well-being, and environmental protection. This blog outlines ten crucial safety measures that LPG plants must follow for safe and efficient operations.
Essential Safety Protocols for LPG Operations
1. Comprehensive Employee Training
All workers handling LPG must receive regular safety training. They should be trained in leak detection, emergency response, and proper handling procedures. Conducting refresher courses and safety drills enhances preparedness.
2. Proper Ventilation in Work Areas
Poor ventilation increases the risk of gas accumulation, which can lead to explosions. LPG plants should have well-ventilated spaces to disperse any leaked gas, reducing potential hazards.
3. Routine Equipment Inspections
Regular maintenance of pipelines, storage tanks, and valves prevents leaks and corrosion. Automated leak detection systems can further enhance safety by providing real-time alerts.
4. Explosion-Proof Electrical Systems
All electrical equipment in an LPG plant must be explosion-proof to prevent sparks from igniting leaked gas. Proper grounding and the use of flameproof fixtures are essential.
5. Automatic Emergency Shut-Off Systems
Automated shut-off valves play a vital role in stopping gas flow during a leak. These systems should be regularly tested to ensure they function correctly in an emergency.
6. Fire Safety Implementation
LPG plants must have adequate fire suppression systems, including fire extinguishers, sprinklers, and fire-resistant barriers. Employees should be trained to use these systems efficiently.
7. Continuous Gas Leak Monitoring
Installing gas detection sensors at critical points ensures early leak detection. These systems provide instant alerts, allowing quick action to prevent serious incidents.
8. Safe Storage and Handling of Cylinders
LPG cylinders should be stored upright, away from heat sources, and in a well-ventilated area. Employees should follow correct lifting and transportation techniques to avoid damage.
9. Well-Defined Emergency Response Plan
Every LPG plant should have a structured emergency response plan that includes evacuation procedures, first aid measures, and coordination with local fire services. Conducting regular drills improves emergency preparedness.
10. Personal Protective Equipment (PPE) Enforcement
Wearing PPE, such as flame-resistant suits, gloves, and protective eyewear, minimizes exposure to hazardous conditions. All workers must follow PPE guidelines strictly.
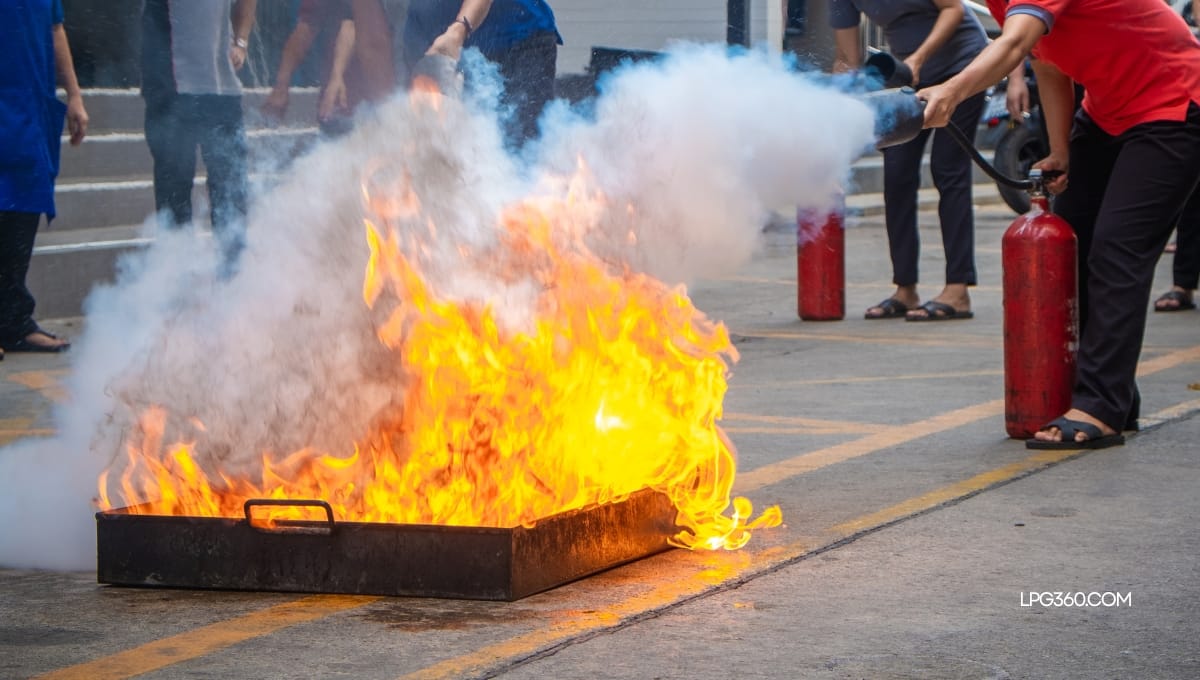
Conclusion
Ensuring safety in an LPG plant is not optional—it is a necessity. By following these ten safety protocols, plant operators can prevent accidents, protect employees, and maintain a secure work environment. Consistent training, regular inspections, and emergency preparedness are essential components of a strong safety culture. A proactive approach to safety not only prevents disasters but also enhances operational efficiency and compliance with industry regulations. Prioritizing safety today ensures a sustainable and risk-free future for LPG operations.
Stay proactive about safety! Implement these protocols today to create a risk-free LPG plant environment.
#LPG #LPG360 #LPGSafety #WorkplaceSafety #IndustrialSafety #LPGHandling #EmergencyPreparedness #GasLeakPrevention #HazardousMaterial #LPGPlant #FireSafety #ExplosionPrevention #SafeOperations #RiskManagement #LPGStorage #HSE #PPE #SafetyProtocol #GasDetection #WorkplaceHealth #HazardPrevention #EmergencyResponse
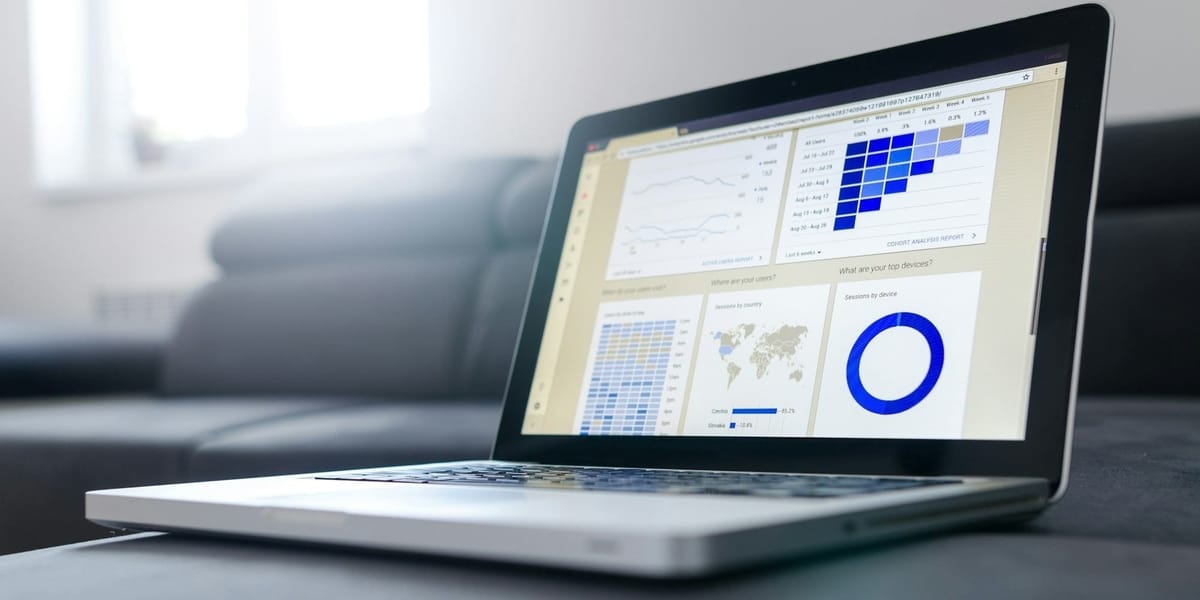